
Types of Industrial Robots! In the current dynamic manufacturing sector, industrial robots are essential in boosting production, efficiency, and accuracy. These automated devices may carry out various duties, from straightforward assembling to complicated machining. The use of industrial robots has grown in significance as sectors aim for improved efficiency and lower operating costs.
Because industrial robots come in a variety of forms, producers may select the one that best meets their requirements. Due to its unique characteristics and capacities, each type of robot could be used in a variety of applications. Every robot is programmed to perform a specific task. In this article, we will discuss some types of industrial robots that help people complete their tasks more efficiently. Here we go!
Articulated Robots
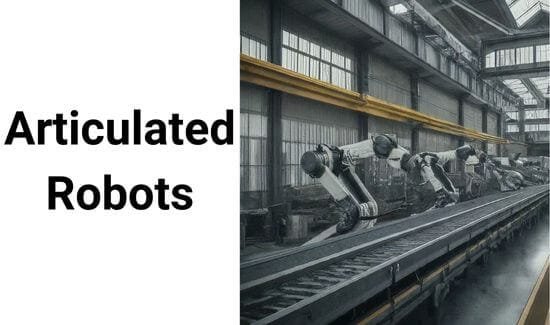
Description
The rotational joints that articulated robots contain enable them to move in a variety of directions, much like the arm of a human. These robots have a great deal of flexibility and variety because, depending on the structure, they even have 2 to 10 joints.
Rewards
The unique performance of articulated robots to function in varied situations is one of their most remarkable qualities. They can do complicated tasks requiring precise motions because of their considerable approach to flexibility. Their large range of motion makes it possible for them to operate effectively across multiple planes, which makes them even better in a variety of manufacturing operations.
Uses
Several applications make considerable use of articulated robots, such as:
Assembly: They are superb at quickly and accurately assembling parts, which results in decreased manufacturing time.
Welding: Their capability to reach challenging angles renders them ideal for welding jobs, guaranteeing durable and uniform welds.
Material handling: By making it simple for these robots to manage and transport heavy goods, manufacturing companies can optimize their operations.
Machine tending: Highly precise components loading and unloading may be carried out by articulated robots.
Packaging: They can wrap goods well thanks to their dexterity, which lowers the possibility of harm occurring in the process.
Cartesian Robots
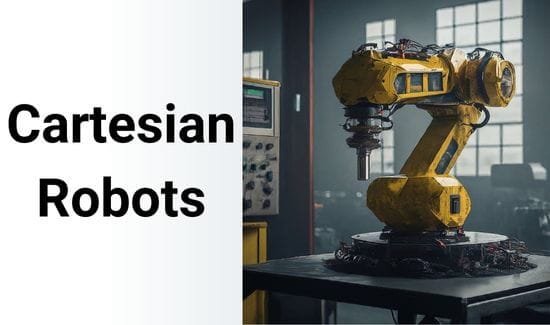
Description
Robots that are Cartesian, or linear, function along the X, Y, and Z perpendicular axes. Their straightforward layout enables accurate linear motion, which makes them suitable for high-accuracy operations.
Benefits
Cartesian robots have a number of benefits, one of which is their superior precision. Because they are simple to program, they can be effortlessly set up and fitted into current manufacturing processes with ease. They are also perfect for a range of applications, from straightforward jobs to more complicated processes, due to their capacity to manage enormous payloads.
Uses
Cartesian robots are useful in many different contexts, such as:
Select and Arrange Tasks: They significantly boost efficiency while grabbing goods from one point and submitting them to another because of their exactness and quickness.
Material handling: When moving bulky items around a workstation, these automated machines help relieve the physical strain on employees.
Machine tending: Robots, like articulated robots, are capable of to load and unload machinery in order to maintain an ongoing workflow.
CNC Machines: Precise motions are required for shaping and cutting materials, and accuracy is vital for running CNC machines.
3D Printing: They often be very helpful in 3D printing applications, where the ability to follow predefined pathways is essential to create complex designs.
SCARA Robots

Description
Selective Compliance Articulated Robot Arms, or SCARA robots in simple terms, are composed of four dimensions that alert them to roam in a horizontal plane while staying rigid in a vertical one. They are a popular option in a range of production applications because of their distinctive configuration, which makes them effective in performing work that calls for both rapidity and accuracy.
Benefits
There are plenty of advantages to using SCARA robots:
Quick and Accurate Movements: They are great for high-speed applications thanks to their layout, which enables fast cycle durations and amazing positioning precision.
Compact Size: Because SCARA robots are lightweight, they may fit into restricted locations without needing considerable setup modifications.
Cost-Effective: Compared to other commercial robot types, SCARA robots are often more economical due to their simpler design and reduced production expenses, like a 6-axis robot.
Applications
We use SCARA robots in a variety of industries, for tasks like:
Assembly of Small Parts: They are outstanding at activities requiring precision assembly, such as implementing components, and compressing screws in electronic production. Material Handling: Because of their precision and speed, they can be useful for moving goods along production lines. Pick-and-Place Operations: By skilfully picking up and arranging elements, SCARA robots boost assembly line productivity. Packaging: They are often utilized for jobs demanding the precise and fast wrapping of products for delivery.
Delta Robots
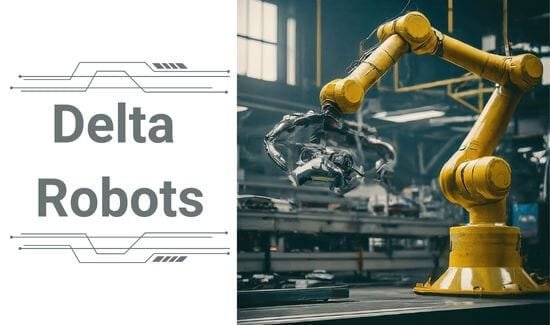
Description
The spider-like framework of delta robots, consists of three limbs joined by a single base, is what earns them their name. They are very helpful in a range of applications, as the way they are constructed, enables tight control over the end output and high-speed motions.
Advantages
High-Speed Operation: Lightweight construction, and swift motions, are excellent for jobs that demand quick cycle times.
Accurate End Effector Control: Delta robots have an elevated level of positioning precision, which is crucial for applications requiring accuracy.
Uses
Delta robots are often used in the following tasks:
Pick-and-Place: Due to their quickness and precision, these robots are ideal for quickly selecting objects from one area and organizing them in another.
Packaging: Because they can handle things with efficiency and without risking harm, delta robots are frequently used in packaging applications.
Food Processing: They work in the food processing sector doing things like packing and categorizing goods that are delicate.
Pharmaceuticals: High-accuracy and hygienic jobs are another field where delta robots serve in the chemical industry.
Cylindrical Robots
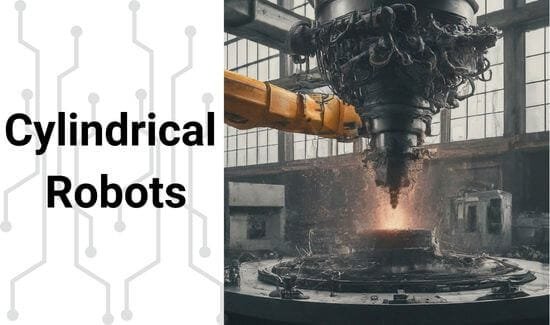
Description
Using a mix of rotary and linear joints, cylindrical robots can move within a cylindrical work envelope. They may occupy a variety of postures within their circular workplace thanks to this design.
Benefits
Following are a few pros of cylindrical robots:
Design Impact: As of their design, they can effectively utilize the available space in small workstations.
Versatility: Because they can move in many directions, cylindrical robots can accomplish a wide range of jobs.
Uses
Typically, cylindrical robots are employed in the following tasks:
Assembly: They work well in assembly jobs where precise component positioning is required.
Machine tending: To maintain a smooth production flow, cylindrical robots are capable of loading and unloading equipment.
Coating: They are ideal for coating applications, like painting, and applying adhesives because of their capacity to work in different angles.
Polar Robots
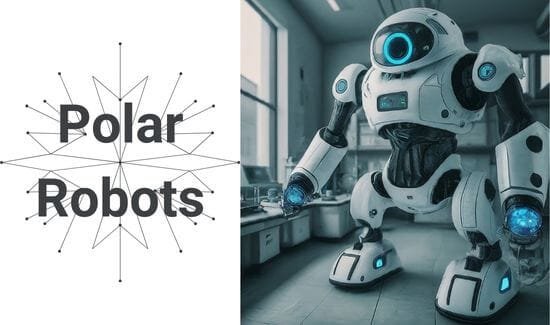
Description
A polar robot, sometimes called a spherical robot, is a special kind of industrial robot, composed of one linear joint with two rotating joints. Their design gives them an extensive amount of flexibility and a large range of motion throughout a spherical coordinate system.
Benefits
Polar robots provide the following advantages to consider:
Flexible Movement: They are ideal for activities in restricted spaces because of their spherical work envelope, which enables them to reach around obstructions.
High-Speed Operation: Polar robots work well for applications requiring fast cycle times because of their ability to move quickly.
Good Lifting Capacity: Due to their strong joints and ever-lasting design, these robots are able to lift heavy objects.
Applications
Polar robots are widely employed in many different sectors for jobs like these:
Die Casting: They boost manufacturing efficiency, making it easier to insert materials precisely in the molds.
Infusion Moulding: They are perfect for handling intricate molding techniques because of their capacity to work in limited locations.
Adaptability: Polar robots work well in welding operations because of their adaptability, which enables them to operate in places that are difficult to access.
Material handling: By effectively transporting goods throughout a workstation, they maximize the flow of production and logistics.
Cobots: Collaborative Robots
Description
Cobots, or collaborative robots, are made to operate securely alongside people in a range of assembly and industrial settings. They have modern safety measures that guard against mishaps and promote output.
Advantages
The following are the primary perks of cobots:
User-Friendly: Cobots are relatively easy to program and operate, even for the ones with limited technical skills, because of their basic interface designs.
Safety Features: Cobots may collaborate closely with human personnel without constituting a serious risk all thanks to the integrated sensors and force-limited joints.
Adaptability: Cobots offer flexibility in manufacturing as they can be reprogrammed easily and redeployed for multiple purposes.
Uses
Cobots are being used in increasing numbers in a variety of applications, including:
Assembly: They support the method of assembling parts, increasing productivity and guaranteeing security.
Quality Inspection: By assisting human workers with checks, these bots can significantly increase accuracy with a few mistakes.
Machine tending: They keep an ongoing workflow rolling by loading and unloading machines.
Pick-and-Place Operations: Moving an object from one place to another is a task that cobots can perform while maintaining accuracy and precision.
Palletizing: They make it easier to order items evenly on pallets for transportation and storage.
Mobile Robots

Description
With the help of wheels or tracks, mobile robots may move freely across a variety of locations. They are flexible enough in their design to move materials across great distances.
Benefits
Among the benefits of mobile robots are:
Flexibility: They are able to navigate through intricate settings, adapt the layout changes, and other obstacles very easily.
Material Transportation: By effectively moving items around sizable facilities, mobile robots can minimize the demand for manual labor.
Uses
Mobile robots are extensively employed in several industries for jobs like these:
Material Transportation: Improves logistics and lowers operating expenses by moving items inside warehouses.
Warehouse Automation: By moving around storage facilities on their own, mobile robots simplify inventory management.
Floor Cleaning: They are used to keep huge areas like factories and shopping malls for cleaning and to maintain hygiene.
Evaluation and Choice
Many aspects should be seen while determining the best kind of industrial robot for a certain application, including:
Speed: Determine the necessary cycle times and choose a robot that can fulfill them.
Reach: Establish the required working envelope and make sure the robot can function well in that area.
Payload Capacity: To make sure the robot can bear the necessary load, measure the objects it will be managing.
Accuracy: Take into account the tasks’ required degree of precision and pick a robot capable of meeting it.
Tips for Integrating Robots:
Determine Workflow Needs: Examine current processes to find places where robots must boost productivity.
Make a plan for training: To get the most out of new robotic systems, make sure individuals have the necessary knowledge to operate them.
Track Performance: Track and analyze robot performance as time passes to identify areas for improvement and organization.
Conclusion
In conclusion, firms looking to increase productivity and efficiency in their operations must have a solid grasp of the many types of industrial robots. Every kind of robot—from collaborative and transportable to articulated and SCARA—offers special benefits suited to certain uses. Through a thorough assessment of their processes’ requirements, companies may choose the best robotic solutions to streamline operations and save expenses. The future of manufacturing will be shaped by the integration of these sophisticated robotic systems, which will stimulate industry innovation and competitiveness as technology advances. Using the appropriate industrial robots to embrace automation will surely create a production environment that is more productive and efficient.